Go To:
- Thermal Processing in Thermocoil Heat Exchangers
- Thermocoil Heat Exchangers Advantages
- Thermocoil Heat Exchangers Description
- Thermocoil Heat Exchangers Secondary Flow Pattern
- Temperature Profile Comparison of Heat Exchangers
- Comparison of Heat Exchangers
- Price Comparison of Heat Exchangers
- Thermocoil Heat Exchanger Drawing
Thermal Processing in Thermocoil Heat Exchangers
The design of the THERMOCOIL is based on the principle of secondary flow or Dean Effect which creates turbulence in products processed in a continuous coiled tube. THERMOCOIL Heat Exchangers are used as heaters, coolers, and holding tubes. The units are manufactured with special tooling to form an helical coil without wrinkling or flattening of the tube.
The flow of the fluid through a curved pipe or coil creates a secondary circulation of fluid called the double-eddy or Dean Effect taking place in a plane perpendicular to the main flow. The nature of the flow of liquids in bends has been thoroughly investigated and many interesting facts have been discovered. For example, when a fluid passes around a bend in either laminar or turbulent flow, a condition known as "secondary flow" is established. This rotating motion of liquids flowing through coiled tubes develops a characteristic swirling action. The frictional resistance of the tube walls and the action of centrifugal force combine to produce this rotation. The degree of secondary flow produced is a function of the ratio of the curvature of the coil to the tube diameter (r/D) and the flow velocity. The faster the velocity of a fluid for a given r/D ratio, the greater the centrifugal force and the more prominent is the secondary flow.
THERMOCOIL Heat Exchangers take advantage of the secondary flow phenomenon to achieve better heat transfer during thermal treatment of products. In the case of particulate products, the continuous rotation of particulate allows uniform heating at the core of the particle as well as the carrier surrounding it. In a viscous product, the swirling motion of the fluid overcomes boundary layers built up at the walls. Thermal processing of products through an helical coil is very effective in reaching uniform temperatures across the tube; thus preventing overprocessing of fluid and viscous products due to faster flow in the center of tube versus zero velocity at the walls.
One benefit of secondary flow in heat processing of fluid or viscous products is effective mixing and suspension of solid particles without mechanical agitation. THERMOCOIL Heat Exchangers have no mechanical induced action. The mixing action is naturally occurring due to friction and centrifugal forces. The particles are gently moved in a circular forward motion clear of any impact due to protrusions in the tube. Thereby, the particle identity is preserved throughout the thermal process.
One of the major benefits from processing in THERMOCOIL is that, there is no source of contamination. The stainless steel coiled tube has no gaskets and no moving parts, thus eliminating any possible microbiological growth or bacteria migration due to crevices, concealment, or connecting materials. Therefore the processing risks of contaminating the product are nonexistent. Moreover, because the coil is made up of a continuous stainless steel tube, the cleaning process, CIP, is very effective and simple.
Back to Top
Thermocoil Heat Exchangers Advantages
- HIGH HEAT TRANSFER COEFFICIENT - secondary flow phenomenon
- HIGH EFFICIENCY - very high media to product flow ratio
- PRACTICALLY NO MAINTENANCE - no moving parts, no gaskets
- EQUIPMENT STERILITY - continuous coil, no crevices
- UNIFORM TEMPERATURE - patented radius to diameter ratio
- MINIMUM OPERATION COST - ease of cleaning and control
- PARTICULATE INTEGRITY - natural mixing, no mechanical protrusions
- PRESERVATION OF SENSITIVE PRODUCTS - high temperature short time
- EQUIPMENT SAFETY - shell rating 150 psi
- GOOD PRODUCT MIXING - centrifugal forces, secondary flow
|
Back to Top
Thermocoil Heat Exchangers Description
DESCRIPTION
Thermocoil Heat Exchangers are made out of Stainless Steel helical coiled pipe, SS baffles, a SS outer skin, a carbon steel outer shell (ASME code 150 psi), and an inner carbon steel core.
The media flow is counter-current to the product flow. The coil is completely surrounded by the media. The shell is insulated and covered with an SS outer skin. The SS outer skin is welded to the top flange leaving the bottom unwelded to allow movement for expansion and contraction due to temperature variation. The flanges are bolted ASME type. The coiled pipe size and length vary based on the application. Due to its design, THERMOCOIL Heat Exchangers can be installed in an outdoor environment as well as indoors.
SYSTEM DESIGN
A system consists of a series of heat exchangers as Preheater, Heater, Holder, Precooler and Chiller. With the exception of the Holder, the Heaters and the Coolers have the same design as described above. Although the basic design remains the same for the Holder, it does not have a pressurized media shell. Its design with a minimum pitch of 0.25 inch per foot meets the USDA approval for holding pasteurized products. The holding tube is fully insulated and covered with SS outer skin.
A system can comprise of several units arranged in parallel or in series depending on the application. For special application the pipe material can be made of Titanium, Hastolloy, Inconel, etc.
CIP and STERILIZATION
The CIP procedure for the THERMOCOIL follows a standard food industry method starting with a cold water rinse, a washing solution, a water rinse, a caustic solution, and finally an acid solution. The noncorrosive materials of the THERMOCOIL can sustain any conventional cleaning procedures. Because the coiled pipe is made of stainless steel, the cleaning, sanitization, and the sterilization processes are simple.
For the sterilization procedure, pressurized hot water 250 degrees F to 300 degrees F is circulated through the coil for a predetermined time. All processing surfaces are in contact with the hot water. Since the units are totally insulated, the sterilization temperature is reached rapidly. After the sterilization time has been satisfied, the units are cooled by introducing cooling media to the jacket of the THERMOCOIL Coolers.
EXPANSION and CONTRACTION
The design of the THERMOCOIL takes into consideration expansion and/or contraction of the coiled pipe due to linear expansion and contraction with temperature changes. In some cases, the length of a steel pipe will increase four inches for every 100 feet of pipe length. The coil is specially designed to eliminate problems associated with start-up or shut-down when the product pipe is exposed to a large temperature differential in a short time.
Back to Top
Thermocoil Heat Exchangers Secondary Flow Pattern
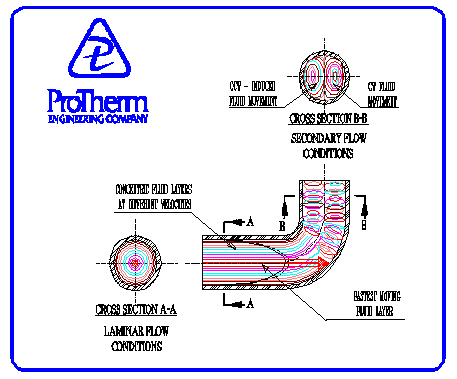
Back to Top
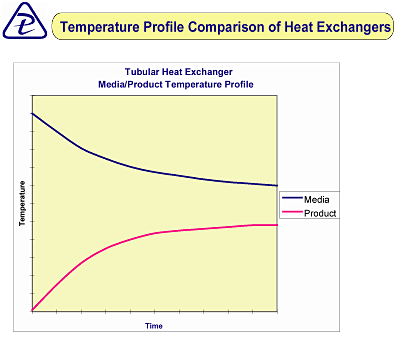
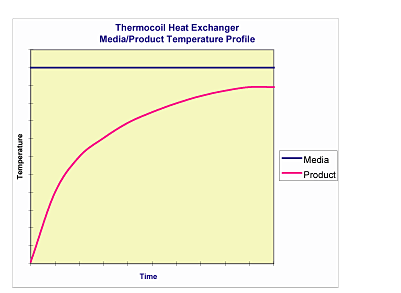
Back to Top
Back to Top
Price Comparison of Heat Exchangers
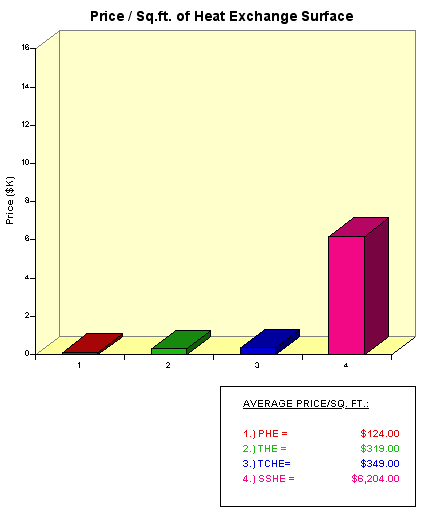
Back to Top
Thermocoil Heat Exchanger Drawing
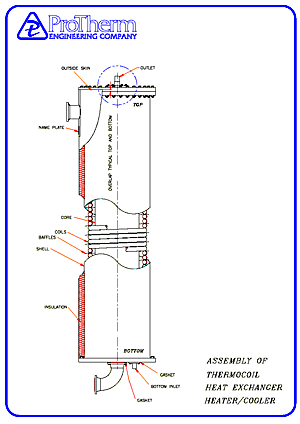
Back to Top
Home | Photo Album | Product Information | Contact Us
|